Les promesses de tenue mécanique attendues du Titane additif sont bien au rendez-vous, et notamment sa tenue en fatigue.
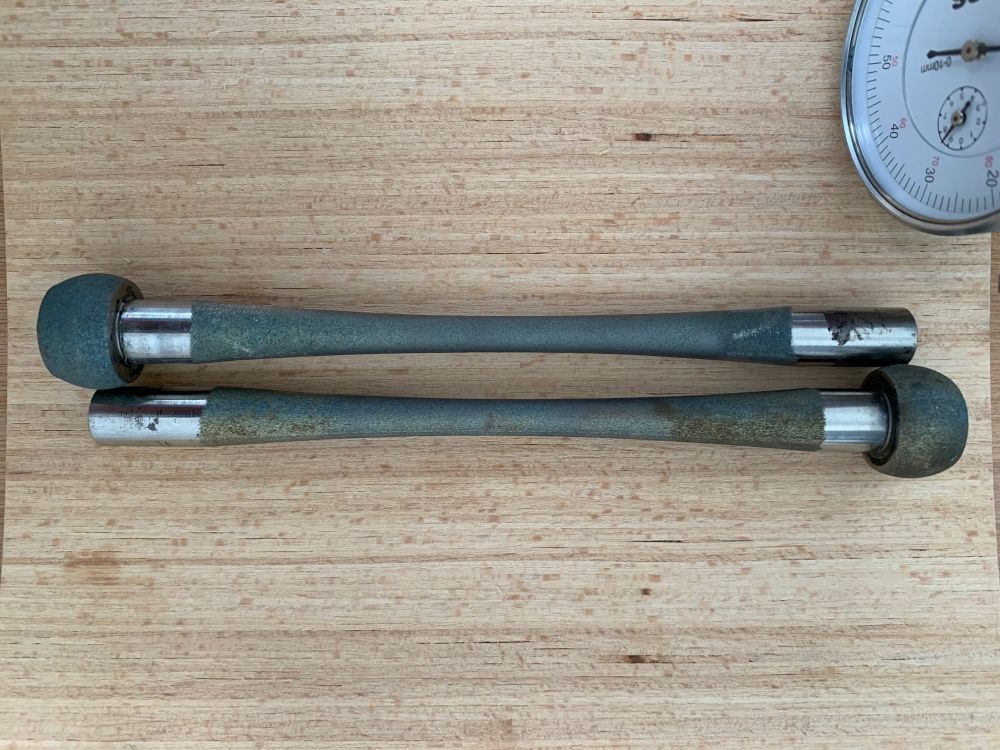
Pourquoi Mécastyle réalise des essais en fatigue?
L'activité de Mécastyle consiste à concevoir des pièces et structures qui doivent offrir à leurs utilisateurs une certaine durée de vie en fonction des efforts subis, ce que nous appelons la tenue en fatigue. En effet, personne ne serait satisfait d'un mécanisme défaillant après seulement quelques cycles d'utilisation… Cependant, afin d'anticiper par simulation numérique les modes de défaillances des pièces que nous concevons, nous avons besoin de connaître le comportement des matériaux pour prédire par calcul de structure le temps (ou nombre de cycles) avant apparition de la défaillance sur les pièces. Et cela nécessite donc de tester des éprouvettes sur des bancs d'essais.
Pourquoi réaliser des essais en fatigue sur les matériaux additifs?
- Les matériaux additifs sont obtenus par superposition de couches de poudre de matière soumises au balayage d'un rayonnement LASER (Light Amplification by Simulated Emission of Radiation) dont l'énergie permet de fusionner la matière couche par couche, l'ensemble de la superposition des couches constituant la pièce.
- Ce processus offre une totale liberté de forme mais les caractéristiques mécaniques du matériau obtenu ne sont plus isotropes (identiques dans toutes les directions) du fait de la superposition des couches. On parle de caractéristiques orthotropes : les caractéristiques mécaniques dans la couche fusionnée par le laser étant différentes des caractéristiques mécaniques entre les couches, donc dans la direction perpendiculaire.
- Il devient donc indispensable de disposer de ces caractéristiques mécaniques orthotropes si l'on veut concevoir, calculer et prédire la durée de vie des pièces et structures issues de fabrication additive, sachant qu'aucun retour d'expérience quant à la tenue en fatigue des matériaux additifs n'est aujourd'hui disponible.
Pourquoi réaliser des essais en fatigue sur le TITANE issu de fabrication additive?
Le Titane issu de fabrication additive offre un compromis technico-économique très favorable par rapport aux autres matériaux quand notamment les contraintes mécaniques subies par les pièces sont très élevées. Pour ordre d'idée, le Ti6Al-4V (Ti grad5) offre un potentiel de tenue mécanique 4 fois plus élevé qu'un aluminium (AS7G06 par exemple) pour un coût matière 2.5 fois plus élevé, sans compter ses caractéristiques physico-chimiques et sa tenue à la corrosion sous contraintes et caverneuse… L'intérêt de la fabrication additive qui permet toute liberté de formes, va donc consister à n'employer que la matière nécessaire - ce qui est moins le cas avec les processus industriels traditionnels - tout en orientant judicieusement la pièce dans l'enceinte de fabrication en fonction des champs de contraintes calculés. L'utilisation du Titane issu de fabrication additive se justifie donc pleinement pour une vaste palette de problématiques techniques.
L’objectif de ces essais en fatigue est donc triple :
- disposer des contraintes limites en fatigue afin de concevoir, calculer, optimiser topologiquement les pièces et prédire leur durée de vie.
- réduire le nombre de prototypes à tester sur banc d’essais et donc réduire les budgets correspondants.
- une mise sur le marché de vos pièces série titane dans un compromis coût/délai largement optimisé.
Cette démarche est indispensable pour la fabrication de pièces série.
Après 77 millions de cycles réalisés sur 22 éprouvettes, nous enregistrons déjà les informations suivantes sur plusieurs paramètres :
- La tendance d’une contrainte limite en fatigue qui se dessine pour les éprouvettes synthétisées en horizontal et vertical.
- La localisation des zones d’initialisation de rupture pour celles n’ayant pas atteint l’objectif de 10⁷ cycles (10 millions de cycles).
- L’influence des zones de supportage dans l’initialisation du phénomène de rupture.
- L'influence de l'orientation des couches de matière.
- L'influence de la rugosité (l'état de surface).
Grâce à cette démarche, nous intégrerons donc les conséquences des processus de fabrication additive sur les réponses mécaniques des pièces tout au long du processus de conception et d’optimisation topologique afin de répondre favorablement à votre CDC.
Différents matériaux ont déjà été caractérisés dans notre laboratoire d'essais afin de constituer une famille cohérente pour répondre à un large spectre de problématiques clients :
- Duraform HST de 3DSystems, PA12 chargé à 30% de fibre de verre courte.
- PA12 Multijet de HP.
- Aluminium AlSi7Mg0.6 issu de 2 fournisseurs + comparatif avec des éprouvettes issues de fonderie gravité.
- Polypropylène de Ricoh.
- Ti6Al4V.
Notre partenaire AFU est équipé de plusieurs machines EOS, dont une M280 et une M290 avec laser de 400W et capacité d’enceinte de 250 x 250 x 326mm. Sur ces machines, nous avons réalisé des éprouvettes synthétisées horizontalement et verticalement afin de pouvoir caractériser le Ti6Al-4V en fatigue. Après fabrication additive, les éprouvettes ont été reprises par tournage numérique par AFU, reprise uniquement dans les zones de montage sur banc, à savoir mandrin et roulement.