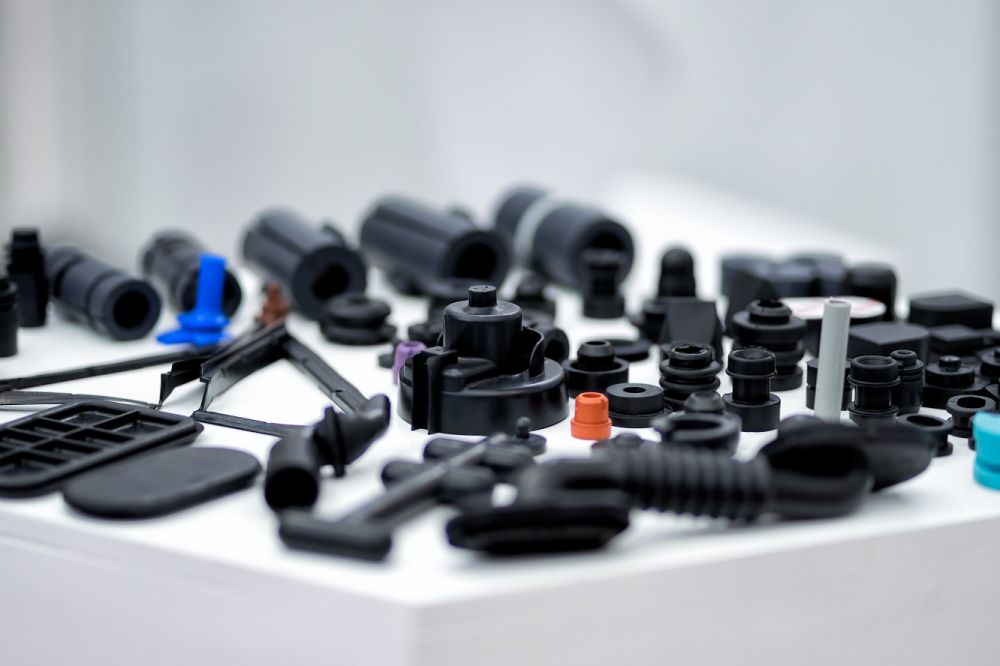
Le géant américain de l’électroménager Whirlpool s’est lancé dans l’utilisation de la fabrication additive pour ses pièces détachées.
Après avoir passé les essais et qualifications internes, la première pièce a pu ainsi être réalisée ; à savoir un bouton poussoir. Celui-ci est fabriqué en PA12, sur une machine HP (technologie Multi-Jet Fusion).
Sur les 11 000 références que compte le catalogue Whirpool, les process de fabrication additive seraient plus économiques pour 7% d’entre elles selon une étude de Spare Parts 3D, le prestataire sélectionné pour la fabrication de ces pièces détachées. Cela représenterait donc plus de 750 références de pièces détachées.
Elles pourront être obtenues via 3 process différents, qui sont le FDM (dépôt de fil fondu), le Multi-Jet Fusion (MJF) de HP et la stéréolithographie (SLA), avec les matériaux suivants : ABS et ABS V0 (FDM), PA12 (MJF) et des résines type PP (SLA).
Le marché de l’impression 3D pour les pièces détachées est en pleine expansion ; il représentera 5% du marché total des pièces détachées dans 5 ans.
En effet, la fabrication additive permet de supprimer les coûts de maintien des outillages, de réduire les stocks de pièces finies et de limiter les immobilisations financières.
La production peut ainsi être réalisée sur demande, sans gestion d’inventaires et à l’unité.
D’autres industriels ont également sauté le pas. Parmi eux, nous pouvons notamment citer le constructeur Volvo, qui a ainsi procédé pour certaines pièces de rechange de sa gamme d’engins de chantiers.